Microreactor de síntesis con reactivos de Grignard
Control continuo del proceso: más rápido, más seguro, más limpio
En 1912, Victor Grignard fue galardonado con el Premio Nobel de Química por su descubrimiento de lo que se conoció como reactivos Grignard. Desde entonces, estos compuestos han llegado a jugar un papel clave en las industrias química y farmacéutica. Ahora, en un desarrollo de los investigadores de Fraunhofer, un nuevo tipo de microreactor no sólo hará que las reacciones con estos reactivos sean más rápidas y seguras, sino que también dará lugar a un producto más puro. Además, el nuevo microreactor es escalable y puede ser operado de forma flexible.
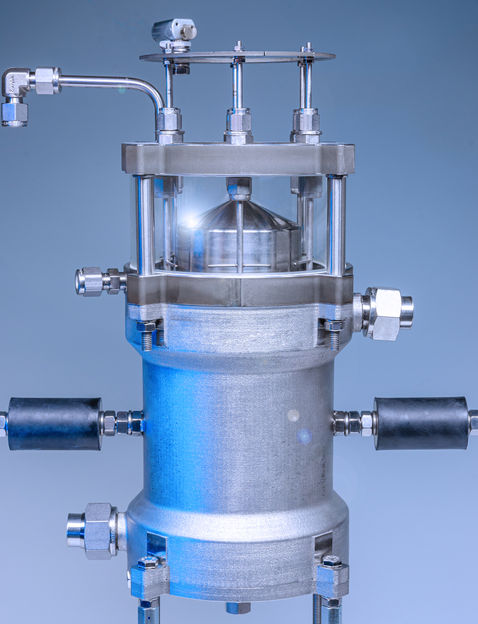
Módulo individual de una planta piloto para la síntesis con reactivos de Grignard.
© Fraunhofer IMM
Muchos de los productos farmacéuticos, fragancias y sabores de hoy en día se producen mediante reacciones con reactivos de Grignard. Descubiertos hace más de 100 años, estos compuestos proporcionan uno de los medios más eficaces para crear enlaces químicos entre los átomos de carbono. Entre los 50 principales ingredientes farmacéuticos activos, uno de cada diez tiene una vía de síntesis que incluye una o más reacciones de Grignard. Sin embargo, hay un inconveniente: dependiendo del tipo de reacción, puede tomar algún tiempo para que la reacción se inicie correctamente y, una vez que lo hace, la reacción genera muy rápidamente mucho calor, que luego tiene que ser disipado. Para restringir la generación de calor, el reactivo sólo se añade al reactor de tanque agitado continuo en porciones limitadas. Esto, sin embargo, alarga el tiempo de reacción, durante el cual se pueden formar muchos subproductos. Si, por ejemplo, el producto deseado reacciona con el material de partida, esto puede dar lugar a la contaminación, con lo que se reduce la calidad y/o el rendimiento del producto.
Control continuo del proceso: más rápido, más seguro, más limpio
Los investigadores del Instituto Fraunhofer de Microingeniería y Microsistemas IMM de Maguncia han logrado eliminar estos problemas. "Hemos sustituido el gran reactor de tanque de agitación continuo por un reactor de flujo", explica la Dra. Gabriele Menges-Flanagan, investigadora del Fraunhofer IMM. "Esto significa que podemos usar toda la potencia de la reacción y aún así controlar la temperatura maravillosamente." Este método tiene una serie de ventajas. Mientras que en el reactor de tanque agitado continuo, la reacción toma mucho tiempo; en el reactor de flujo, todo el reactivo se convierte en cuestión de minutos. Además, la pureza del producto es mayor y las cantidades producidas pueden adaptarse a las necesidades. En otras palabras, el proceso no sólo es más rápido y seguro, sino que también proporciona un producto más limpio.
Estas ventajas se deben al diseño del reactor. Dentro del reactor de flujo, el reactivo - generalmente un bromuro o cloruro orgánico - es bombeado a través de un lecho de virutas de magnesio. La abundancia de virutas de magnesio en el reactor asegura que la reacción se desarrolle correctamente y luego progresa de manera controlada. Aquí también es crucial la geometría del reactor, que cuenta con un cilindro de doble pared, enfriado por dentro y por fuera por un flujo continuo de aceite. Esto asegura que el calor de la reacción se disipe rápida y eficientemente, por lo que no sólo mejora la seguridad sino que también inhibe la producción de subproductos indeseables. El hecho de que tanto el reactivo como el producto fluyan a través del reactor con tiempos de residencia cortos también inhibe las reacciones secundarias. Esto se debe a dos razones: por una parte, el reactivo se convierte rápidamente en producto; por otra, este producto fluye continuamente a través del reactor, en lugar de, como en el pasado, nadar junto con el reactivo en un reactor continuo de tanque agitado. En otras palabras, hay muchas menos oportunidades de que se produzcan reacciones secundarias entre ambos. La abundancia de magnesio en el reactor de flujo también ayuda a prevenir las reacciones secundarias. Esto se debe a que es más probable que el reactivo reaccione con las virutas de magnesio que con el producto, que se elimina rápidamente.
Una planta piloto escalable y flexible
Los investigadores ya han construido una planta piloto, que puede convertir hasta 20 litros de solución de reactivo por hora. Puede funcionar durante períodos cortos o de forma continua, dependiendo del volumen de producto requerido. En caso de que se necesiten mayores volúmenes de producto, otra opción es hacer funcionar varios módulos de reactor juntos. La planta piloto actual consta de cuatro de esos módulos y constituye una importante etapa intermedia en el camino hacia el aumento de la producción y, en última instancia, hacia el logro de la producción a escala industrial. Los investigadores de Fraunhofer ya se han asociado con socios de la industria para llevar a cabo los primeros estudios de viabilidad. "La retroalimentación de la industria ha informado todo el proceso de desarrollo, desde la escala de laboratorio hasta la planta piloto", confirma Menges-Flanagan. También dice que un proyecto piloto con clientes de la industria en su sitio es factible en alrededor de un año.
Además de ser adecuada para la formación de cualquier tipo concebible de reactivo de Grignard, la planta también debería resultar adecuada, a largo plazo, para la síntesis de compuestos organometálicos de zinc. De hecho, los investigadores ya han realizado tales reacciones a escala de laboratorio. Utilizando el nuevo reactor, debería ser posible por primera vez hacer estas reacciones flexibles y escalables.
Nota: Este artículo ha sido traducido utilizando un sistema informático sin intervención humana. LUMITOS ofrece estas traducciones automáticas para presentar una gama más amplia de noticias de actualidad. Como este artículo ha sido traducido con traducción automática, es posible que contenga errores de vocabulario, sintaxis o gramática. El artículo original en Inglés se puede encontrar aquí.