Vetter invests 300 Million Euros
Vetter has announced that in keeping with its commitment to providing customers with the manufacture of high quality drug products, the company will invest approximately 300 million euros to expand and upgrade its manufacturing facilities over an estimated five-year period. As a leading contract development and manufacturing organization, Vetter is continuously developing its manufacturing sites and techniques to prepare them for future needs and requirements. The upgrades are being driven by a changing healthcare market that is affected by issues such as ever-more complex molecules, smaller batch sizes, and increasing regulatory requirements.
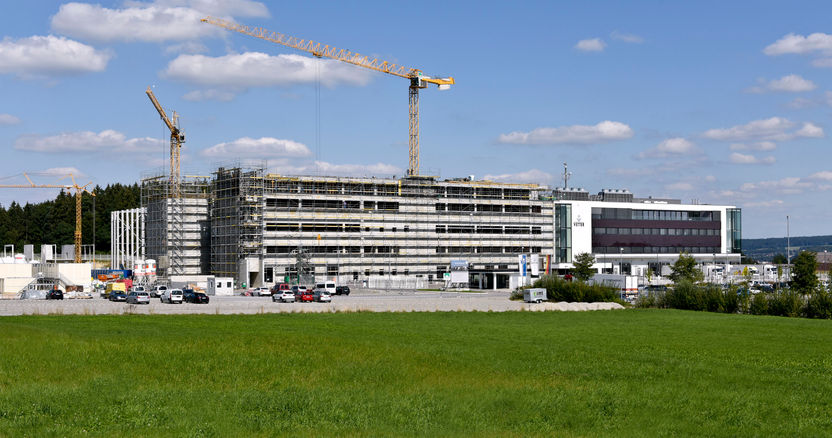
Structural work completed: A portion of the 300 million Euro investment is directed to completion of the Ravensburg Vetter West facility expansion.
Vetter Pharma International GmbH
The first of the facility expansions are already ongoing at several of the company’s German locations including its ‘Ravensburg Vetter West’ center for visual inspection and logistics. Structural work for the facility enlargement, which will offer more than double of its current capacity, is completed with the site being on schedule to become fully operational in 2017. In addition, the Ravensburg Vetter South production site has also been designated for significant enlargements as is the Ravensburg Schuetzenstrasse facility where initial construction activities began in 2013. All three site expansions will result in additional capacities for drug product manufacturing and logistic sevices.
A central technology element of the planned upgrades will be the implementation of an in-house made improved restricted access barrier system (RABS) concept which will contribute to increased operational excellence in aseptic manufacturing. For decades, Vetter has relied on RABS as one of the two distinct technologies available today for its aseptic filling processes, the other being isolators. RABS achieves the sterility assurance level (SAL) required by regulatory authorities, and allows for rapid product change-over coupled with high safety. To better meet future industry trends in quality, safety and flexibility, a corporate project team has evolved this ‘Improved RABS concept’ by combining the advantages of isolator and RABS technology. The core of the approach is a uniquely fast, by today’s standards, 3-hour cycle and fully automated decontamination of the cleanroom using hydrogen peroxide (H2O2), resulting from an extremely high level of process innovation. Following a successful pilot project in a selected cleanroom the company will now implement this decontamination concept in all of its cleanrooms within the next years.
Most read news
Other news from the department business & finance
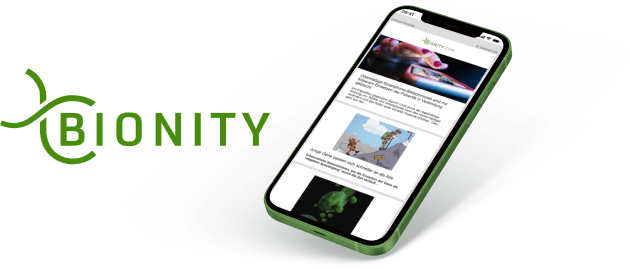
Get the life science industry in your inbox
By submitting this form you agree that LUMITOS AG will send you the newsletter(s) selected above by email. Your data will not be passed on to third parties. Your data will be stored and processed in accordance with our data protection regulations. LUMITOS may contact you by email for the purpose of advertising or market and opinion surveys. You can revoke your consent at any time without giving reasons to LUMITOS AG, Ernst-Augustin-Str. 2, 12489 Berlin, Germany or by e-mail at revoke@lumitos.com with effect for the future. In addition, each email contains a link to unsubscribe from the corresponding newsletter.