Using nature as a model for low-friction bearings
lubricants are required wherever moving parts come together. They prevent direct contact between solid elements and ensure that gears, bearings, and valves work as smoothly as possible. Depending on the application, the ideal lubricant must meet conflicting requirements. On the one hand, it should be as thin as possible because this reduces friction. On the other hand, it should be viscous enough that the lubricant stays in the contact gap. In practice, grease and oils are often used because their viscosity increases with pressure.
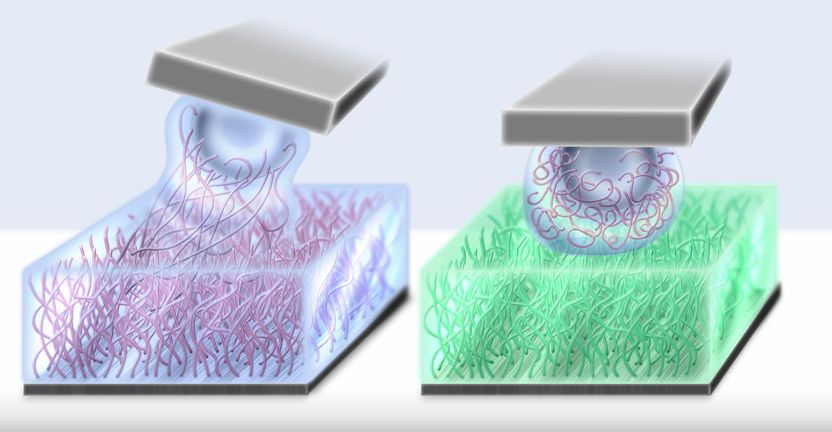
Two different polymers at the contact point (right) prevent the polymers becoming entangled (left).
Nolux Media
Biological lubrication in contrast is much more efficient. In joints, a thin, watery solution prevents friction. The thin film stays where it should thanks to a trick of nature. A polymer layer is anchored to the cartilage at the end of bones. Polymers are a string of densely packed, long-chain molecules. They protrude from the cartilage and form "polymer brushes" which attract the extremely fluid lubricant and keep it in place at the contact point.
Over the last 20 years, numerous attempts have been made to imitate the natural model technically. But with no resounding success. The tentacle-like polymers on surfaces opposite each other tend to get tangled up in each other. They slow each other down and detach from the surfaces. In technical systems, individual polymers that become detached are difficult to replace as they do not possess the same self-healing mechanisms as in a natural organism.
Jülich physicist Prof. Martin Müser came up with the idea of using two different polymers at the contact point to prevent the polymers becoming entangled. "Using supercomputers, we simulated what would happen if we applied water-soluble polymers to one side and water-repellent polymers to the other side," says head of the NIC (John von Neumann Institute for Computing) group Computational Materials Physics at the Jülich Supercomputing Centre (JSC)." This combination of water-based and oil-based liquids as a lubricant reduced the friction by two orders of magnitude – around a factor of 90 – compared to a system comprising just one type of polymer."
Measurements with an atomic force microscope at the University of Twente in the Netherlands verified the results. "The two different phases of the liquid separate because they repel each other. This simultaneously holds the polymers back and prevents them from protruding beyond the borders," says Dr. Sissi de Beer, who recently moved from Müser's group to the University of Twente.
The low-friction two-component lubricant is interesting for numerous applications. One example are simple piston systems, like syringes, which are used to precisely administer even tiny amounts of a drug. Above all, the new process could provide low-friction solutions where high pressures and forces occur locally – for example, axle bearings and hinges. For the most common lubricant – engine oil – an alternative has yet to be found; conventional polymer brushes are unable to withstand the high temperatures.
Original publication
Other news from the department science
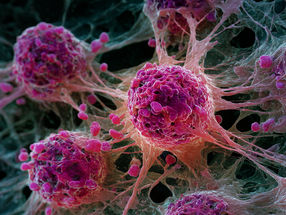
New Label-Free Imaging Tracks Cancer Treatment in Single Cells
One Tool, Many Applications
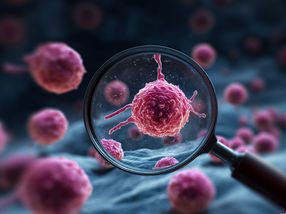
The evolution of cancer cells decoded
"Our vision is a new type of early cancer detection"
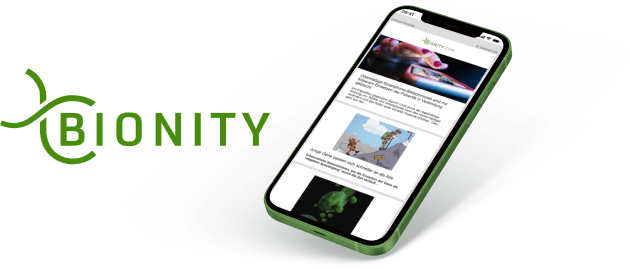
Get the life science industry in your inbox
By submitting this form you agree that LUMITOS AG will send you the newsletter(s) selected above by email. Your data will not be passed on to third parties. Your data will be stored and processed in accordance with our data protection regulations. LUMITOS may contact you by email for the purpose of advertising or market and opinion surveys. You can revoke your consent at any time without giving reasons to LUMITOS AG, Ernst-Augustin-Str. 2, 12489 Berlin, Germany or by e-mail at revoke@lumitos.com with effect for the future. In addition, each email contains a link to unsubscribe from the corresponding newsletter.