Highly efficient production of advanced biofuel by metabolically engineered microorganism
Combining systems metabolic engineering and downstream process, production of butanol could be dramatically increased
Fuels including gasoline, diesel, and jet fuel are derived from fossil oil thorough the petroleum refinery processes. Increased concerns over environmental problems and limited fossil resources drive scientists and researchers to turn their attention to developing fossil-free, bio-based processes for the production of fuels from renewable non-food biomass. Utilizing systems metabolic engineering, a Korean research team at the Korea Advanced Institute of Science and Technology (KAIST) has succeeded in demonstrating an optimized process to increase butanol production by generating an engineered bacterium.
In the paper published in mBio, Distinguished Professor Sang Yup Lee at the Department of Chemical and Biomolecular Engineering, KAIST, Dr. Do Young Seung at GS Caltex and Dr. Yu-Sin Jang at BioFuelChem applied a systems metabolic engineering approach to improve the production of butanol through enhancing the performance of Clostridium acetobutylicum, one of the best known butanol-producing bacteria.
Microorganisms have proven to be efficient biocatalysts for the production of biofuels from various sources of biomass in an environmentally-friendly way. However, the microorganisms isolated from nature are often inefficient for the economical production of desired products at an industrial scale. Thus microorganisms' performance needs to be improved in order to be suitable for the industrial production of biofuels. Systems metabolic engineering, which allows metabolic engineering at a systems-level, is employed for designing and optimizing cellular metabolic and regulatory networks to induce the most efficient production of target bioproducts.
The Korean research team analyzed metabolic pathways leading to butanol production and found that two different solvent-forming pathways can be potentially employed. In one pathway, butanol is directly produced from carbon source, which was termed as hot channel, and in the other, butanol is converted from the acids produced earlier in fermentation process, which was termed as cold channel. Using the in silico modeling and simulation tools, Professor Lee's team demonstrated that the hot channel allowed a much better approach to produce butanol compared with the cold channel. To reinforce a metabolic flux toward the hot channel for butanol production, the metabolic network of C. acetobutylicum strain was systematically engineered.
In addition, the downstream process was optimized and an in situ recovery process was integrated to achieve higher butanol titer, yield, and productivity. The combination of systems metabolic engineering and bioprocess optimization resulted in the development of a process capable of producing more than 585 g of butanol from 1.8 Kg of glucose, which allows the production of this important industrial solvent and advanced biofuel to be cost competitive.
Most read news
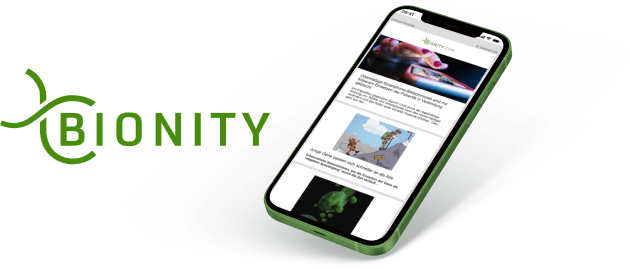
Get the life science industry in your inbox
By submitting this form you agree that LUMITOS AG will send you the newsletter(s) selected above by email. Your data will not be passed on to third parties. Your data will be stored and processed in accordance with our data protection regulations. LUMITOS may contact you by email for the purpose of advertising or market and opinion surveys. You can revoke your consent at any time without giving reasons to LUMITOS AG, Ernst-Augustin-Str. 2, 12489 Berlin, Germany or by e-mail at revoke@lumitos.com with effect for the future. In addition, each email contains a link to unsubscribe from the corresponding newsletter.