Rentschler Manufacturing Facility Wins 2012 Facility of the Year Award in Equipment Innovation
Rentschler Biotechnologie GmbH announced that the company’s new manufacturing facility has won the 2012 Facility of the Year Award (FOYA) in the category Equipment Innovation. The award recognizes Rentschler for its flexible, multi-product manufacturing facility designed to minimize manufacturing costs and product cycle times.
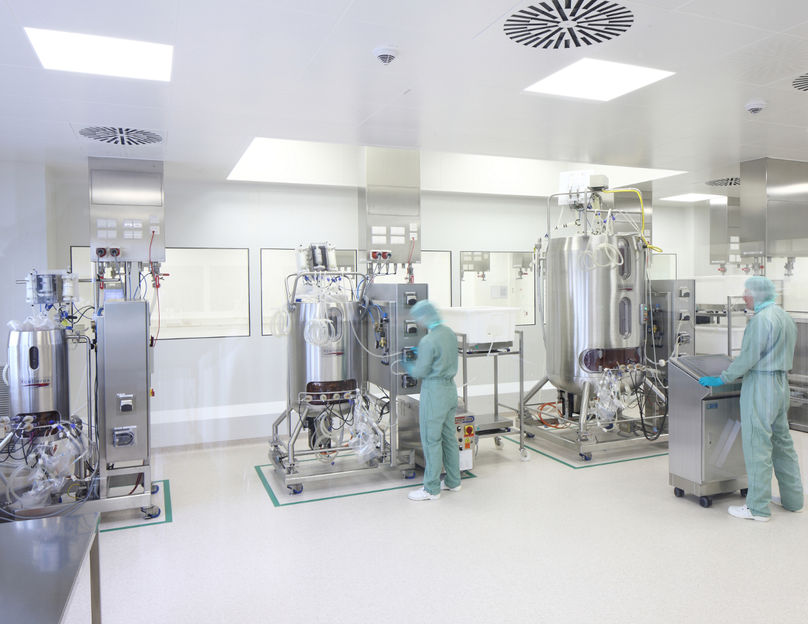
Upstream manufacturing suite with 100% mobile, single-use and ready-to-use manufacturing equipment.
The Facility of the Year Award (FOYA), sponsored by the International Society for Pharmaceutical Engineering (ISPE), INTERPHEX and Pharmaceutical Processing magazine, is the premiere global awards program focused on recognizing state-of-the-art projects utilizing new, innovative technologies to reduce the cost of producing high quality medicines and to improve the quality of products.
The new facility features a flexible space concept comprising independent, connectable all-purpose clean rooms designed for the operation of 100% mobile, single use manufacturing equipment for upstream and downstream processing. Due to the consistent use of single-use equipment, steam-in-place (SIP) and clean-in-place (CIP) operations are obsolete. All clean room suites include connections to the facility-wide data logging system (DLS) system, which is preconfigured for plug and play setup of mobile manufacturing equipment. Further optimization was achieved based on lean logistic and manufacturing principles and the consequent implementation of a visual factory concept.
“Rentschler is honored to receive this prestigious award for expanding its manufacturing facility,” said Thomas Siklosi, Senior Vice President GMP Operations at Rentschler Biotechnologie. “With this award-winning facility, we can offer our clients substantial cost benefits for custom manufacturing of biologics for clinical trials. In addition, the know-how we gained during the expansion project together with our multiple engineering and equipment partnerships will enable us to cost efficiently design and also build dedicated production facilities for market supplies.”
Rentschler’s new manufacturing facility consists of four independent, fully configurable multi-purpose clean room suites to be used with different processes as well as one inoculum suite. The standard configuration is designed for the simultaneous operation of two 1,000 L fed-batch processes. Additional equipment for scale-up (e.g. 2 x 1,000 L or 2,000 L) or alternative processes (e.g. perfusion) can be added. The modular concept allows fast implementation of alternative production equipment according to the customers’ requirements.
Most read news
Organizations
Other news from the department business & finance
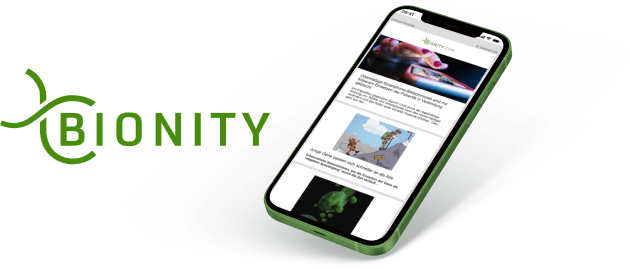
Get the life science industry in your inbox
By submitting this form you agree that LUMITOS AG will send you the newsletter(s) selected above by email. Your data will not be passed on to third parties. Your data will be stored and processed in accordance with our data protection regulations. LUMITOS may contact you by email for the purpose of advertising or market and opinion surveys. You can revoke your consent at any time without giving reasons to LUMITOS AG, Ernst-Augustin-Str. 2, 12489 Berlin, Germany or by e-mail at revoke@lumitos.com with effect for the future. In addition, each email contains a link to unsubscribe from the corresponding newsletter.