Plants instead of petroleum – making new bio-based material solutions tangible on a pilot scale
From laboratory to pilot scale - a rocky road
The INN PRESSME joint project, funded by the European Union with around 14 million euros, was launched three years ago. The aim of the 27 project partners from nine European countries is to establish a Europe-wide ecosystem for the development and production of plant-based, recyclable, and/or biodegradable packaging, energy, and transportation solutions, as well as consumer goods. The planned nine test cases with prototypes have currently been completed, and the results are very encouraging.
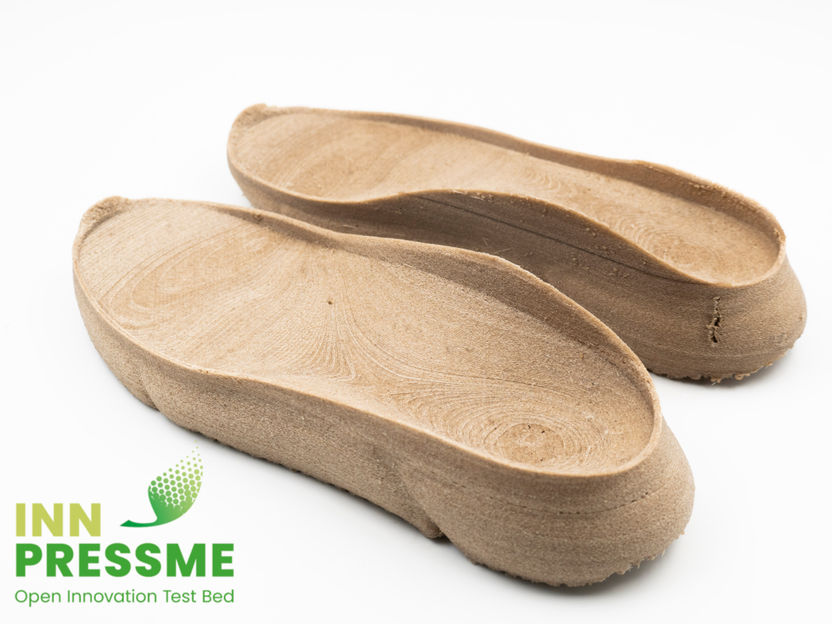
Antimicrobial coating on 3D printed shoe soles. Aitiip, Podoactiva, IWN, Fraunho-fer ISC and IPC were in-volved in the development.
Aitiip/INN PRESSME
The European Green Deal has set out a roadmap and an ambitious package of measures to create a sustainable and green European economy with zero net emissions by 2050. The European Union also supports the realization of a cleaner and competitive Europe in cooperation with economic actors, consumers, citizens, and civil society organizations through its HORIZON research program, in which INN PRESSME is funded. INN PRESSME offers a two-pronged approach to help European companies achieve ambitious climate targets.
On the one hand, plant-based raw materials are to be developed for new marketable products and goods that are also recyclable. Thanks to nanotechnology, these materials should achieve and even surpass the performance of current fossil-based materials.
Secondly, digitalization is to be supported by providing companies with all the data and tools for modeling the life cycle value chain that are compatible with the conversion of industrial production – from raw material conversion to material processing. This is the key to maximizing the use of raw materials in the circular economy, which is also accompanied by extensive LCA, LCCA, and LCI studies.
The total of nine test cases for pilot production in very different sectors have been completed as planned after three years of the project. The production of demonstrators from bio-based materials for environmentally friendly packaging, energy, transportation, and consumer goods was successfully demonstrated on a pilot scale. For this purpose, existing pilot plants were expanded with project funds and adapted to the new requirements.
In the INN PRESSME project, the Fraunhofer Institute for Silicate Research ISC took on the challenging task of preparing the products made from plant-based raw materials with special bio-based functional coatings for their respective requirements in use. The Fraunhofer ISC was involved in a total of six test cases. The institute modified the bioORMOCER® materials, which were designed as barrier layers for the packaging sector. In addition to barrier layers for paper-based packaging, scratch-resistant and optical layers for automotive applications were produced by using these special ORMOCER® materials. Antimicrobial and easy-to-clean coatings for sports products and shoe soles were also developed.
From Laboratory to Pilot Scale - A Rocky Road
What works in the laboratory does not necessarily achieve the same result on a production scale. Scaling up the quantities of material produced therefore takes place in defined steps to make the necessary adjustments to the material formulation and manufacturing process. At the Fraunhofer ISC, this upscaling was carried out up to pilot scale. For example, a 100-liter reactor for lacquer synthesis and a roll-to-roll system were used to apply the barrier layers to a nanolayer-modified paper. Due to the low layer thicknesses required, 100 liters is sufficient for up to 3,000 square meters of coated surface. A particular challenge in the development of the coating formulation was to match the coatings to the quality and requirements of the respective bio-based substrates. The properties had to be adapted very individually, as bio-based materials, in particular, have complex surfaces and are not very temperature-stable or resistant to chemicals. The processing of bio-based materials in roll-to-roll processes is also often challenging, and the expected cycle rates are often only achieved with further adaptation.
However, despite all the technical challenges, the successfully completed test cases proved that the establishment of a Europe-wide pilot plant network in various institutions has been successful, and that cooperation in the various work steps works smoothly.
Well-Established Infrastructure for Companies
In future, this pilot plant network will be available to companies via a Single Entry Point (SEP). This will provide them with effective support in upscaling their own bio-based solutions with an excellently developed infrastructure, without having to invest in their own plants. INN PRESSME thus significantly reduces the entrepreneurial risks until new plant-based products are ready for the market. The final year of the project will now be used to set up the SEP and carry out comprehensive life cycle analyses and end-of-life assessments with regard to biodegradability and recyclability.