Funding dedicated to the development of commercial-scale, fully automated additive manufacturing of resorbable medical implants
BellaSeno and Fraunhofer Institute for Production Technology Receive EUR 1.4 Million BMBF Grant
BellaSeno GmbH and the Fraunhofer Institute for Production Technology IPT announced that both parties have received a grant totaling EUR 1.4 million from Germany´s Federal Ministry of Education and Research (BMBF) under the funding program KMU-innovativ.
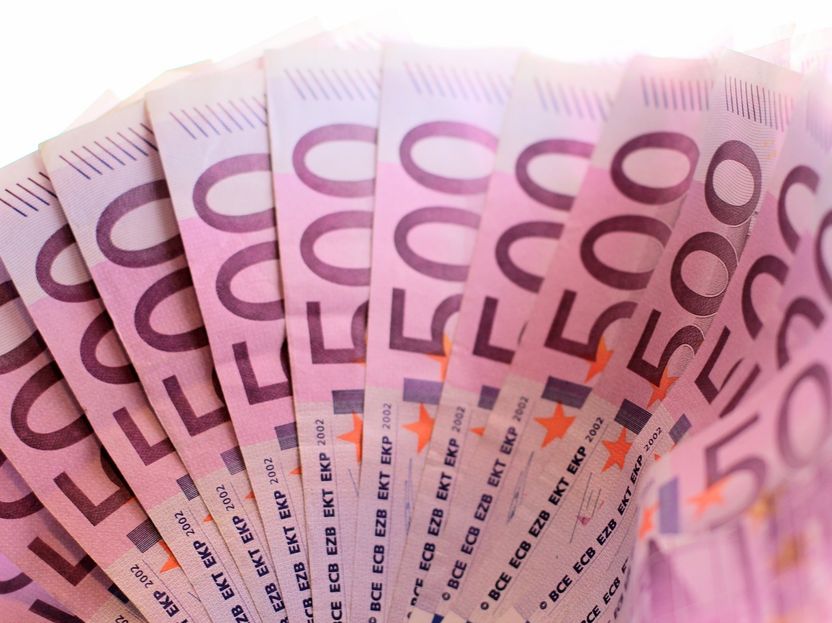
Symbolic image
pixabay.com
BellaSeno and Fraunhofer IPT aim to develop a high-performance industrial scale-up process for its GMP-compliant manufacturing facilities, which include leading-edge features such as high-througput additive manufacturing based on the so-called no-touch approach to significantly improve the safety and sterility of medical implants.
Specifically, the collaboration partners plan to establish a fully automated, commercial-scale manufacturing platform supported by robotic systems and intelligent software which control the polymer-feeding, the implant handling, QC steps, labelling and recording traceability data. This will enable a constant 24-hour manufacturing flow covering all necessary process steps, while minimizing mistakes and optimizing the outcome of the production. With this approach, BellaSeno intends to significantly shorten development and manufacturing times and at the same time enhance the quality of its medical implants.
“So far, the key steps in the additive manufacturing process had to be performed manually,” said Dr. Navid Khani, Head of R&D at BellaSeno. "The BMBF grant and the collaboration with Fraunhofer IPT will allow us to pursue a 3- to 4-fold increase of productivitiy for commercial-scale manufacturing driven by robotics and automation. As soon as we have fully established the new infrastructure, we will be able to create a cloud-based factory which can enable manufacturing at different locations and adapting the design by the push of the button. Such a fully scalable, automated, cloud-based additive manufacturing infrastructure for medical implants has never been established before."
“The joint project combines BellaSeno’s extensive knowledge in 3D-printing high quality absorbable scaffolds and their ingenious Senella implant with Fraunhofer IPT’s vast experience in the development of fully automated cleanroom production facilities,” said Ferdinand Biermann, Head of the business unit “Life sciences engineering” at the Fraunhofer IPT. “A freely moving, autonomous robot, fully networked processing units and an adaptive, service-oriented software structure allow repeatable and high quality manufacturing by maintaining full flexibility in the production process. Not only will the production site make it possible to bring products to market that immensely increase the patient’s quality of care, but it will also set a new benchmark for the automated production of medical implants.”
Other news from the department business & finance
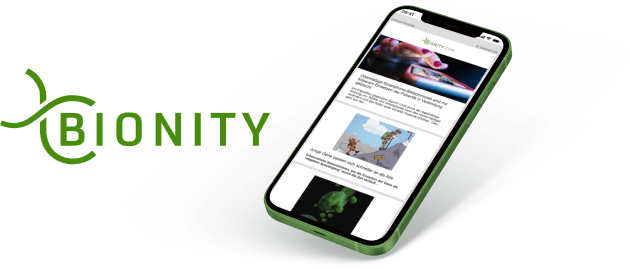
Get the life science industry in your inbox
By submitting this form you agree that LUMITOS AG will send you the newsletter(s) selected above by email. Your data will not be passed on to third parties. Your data will be stored and processed in accordance with our data protection regulations. LUMITOS may contact you by email for the purpose of advertising or market and opinion surveys. You can revoke your consent at any time without giving reasons to LUMITOS AG, Ernst-Augustin-Str. 2, 12489 Berlin, Germany or by e-mail at revoke@lumitos.com with effect for the future. In addition, each email contains a link to unsubscribe from the corresponding newsletter.
Most read news
More news from our other portals
Something is happening in the life science industry ...
This is what true pioneering spirit looks like: Plenty of innovative start-ups are bringing fresh ideas, lifeblood and entrepreneurial spirit to change tomorrow's world for the better. Immerse yourself in the world of these young companies and take the opportunity to get in touch with the founders.